Operation Platform for Large AI Factories

Equipment Connection and Communication Planning
All factory equipment (e.g., cutting machines, production devices, measuring instruments, robotic arms) is connected using MCUs (Microcontrollers) for basic data input and output. To enhance communication efficiency, higher-level industrial protocols such as OPC UA, Modbus, or Profinet should be integrated. Standardized API codes are designed, and IP addresses and ports are assigned to mark communication interfaces. A personified account system is employed to manage devices, allowing for identity recognition and interaction capabilities.
Hybrid Computing and Production Group Planning
Server specifications are chosen based on the number of factory devices, deploying a hybrid LLM (Large Language Model) and LVM (Lightweight Model) computing architecture. LLM is used for analyzing order texts and generating production plans, while LVM handles rapid command distribution. The system personifies each device IP as a user, similar to a social network model. Upon receiving new orders, the main server analyzes the order requirements and production volume, compares them to current equipment capacity, dynamically organizes production groups, and sends production instructions (including program codes and production data) via API to the relevant groups, achieving automated scheduling and collaboration.
Data Collection and Management
Data on equipment functions, specifications, manuals, technical details, and IP addresses are collected, categorized, and entered into an AI model database. SQL technology is used for data management, complemented by distributed or NoSQL databases (e.g., MongoDB, Cassandra) to optimize large-scale data handling. This data supports AI model training, real-time equipment monitoring, and production process optimization.
Automation Challenges and Future Development
Currently, cutting machines like lathes and machining centers lack automatic blade-changing capabilities, requiring engineers to set up tools and perform test runs before production. To achieve full automation, introducing automatic tool insert systems and smart sensors is essential. Industries should consider integrating hardware interfaces with AI technology and design solutions aligned with Industry 4.0 standards to realize a fully autonomous AI-driven factory.
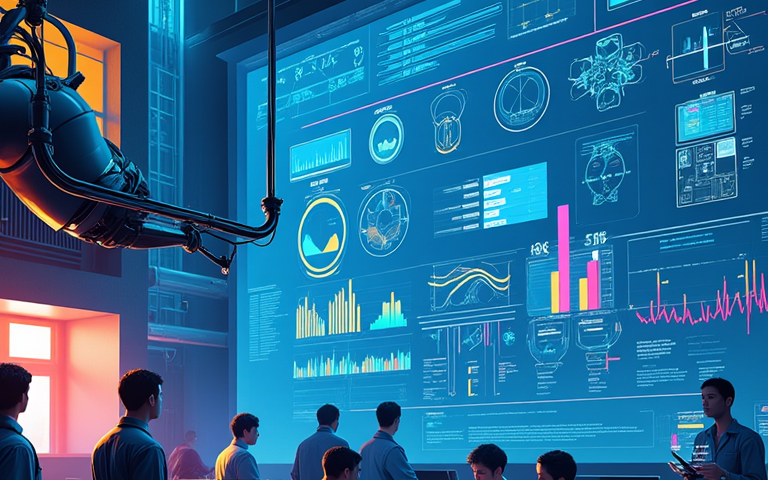
Key Features
From MES to AI-Driven Management
Transition large factories from traditional MES (Manufacturing Execution Systems) to AI-driven management models, achieving equipment integration and process automation.
Personified Production Group Management
Introduce the concept of personified equipment management, using a social network-like group model to enhance production processes. Standardized APIs facilitate collaboration and communication between devices.
Hybrid Computing and Comprehensive AI Management.
Utilize a hybrid of LLM and LVM technologies for order review, engineering analysis, capacity allocation, and delivery management. Future integration with ERP systems will progressively enable end-to-end AI-driven automation from production to finance.
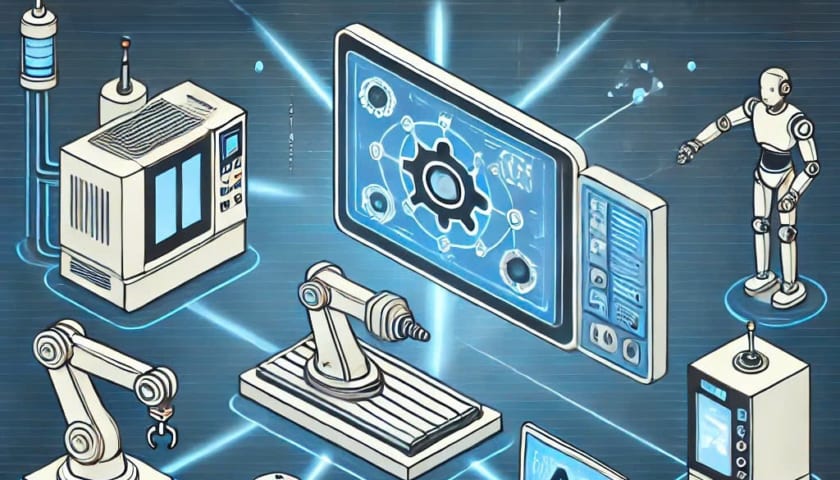
Innovation